Since I'm not sure about the mechanical skill level of everyone on this site, I'm going to start a few "general knowledge" threads of advice for beginners. Some of you will probably already know this, but it might come useful to some people.
Torque Wrench 101.
1. General care and Storage:
When purchasing a torque wrench, be aware to look up the manufacturers tolerance. This should be in a (+/- X%) marking. This means that when you set your torque wrench to a given value (e.g. 350 in/lbs) it will be within a range of that setting (a +/-5% tolerance will be anywhere from 367.5 to 332.5 in/lbs when set to 350 in./lbs). Generally speaking anything more than 3% isn't worth purchasing, as the tolerance tend to enlarge over time.
When storing your torque wrench for any period of time (more than 30 mins is a good rule), do not leave it on the torque value you had last used. Instead bring it to the lowest value on it's rating, NOT ZERO. Bringing it to "zero" can loosen the internals and ruin the torque wrench.
Every manufacturer has a set amount of uses per calibration of torque wrench they make. Keep track of this useage, when you are close to that number, or a year has gone by since purchase (which ever comes first) send it to the manufacturer for calibration. The internals weaken over time and need to be adjusted properly, otherwise your +/-2% wrench will become a +/- 10%.
Do not, and I repeat do not DROP even onto a table your torque wrench, even a 1" fall can loosen components and make the wrench un-usable. If dropped accidently, send the unit in for calibration.
2. Proper Application.
When choosing to use your torque wrench, make sure that the wrench is able to stay within torque range. Using the Wrench example as above, a nut that is required to be torqued to 340-360 in/lbs would require a different wrench than above, as the wrench can either over-torque or under-torque the nut and cause pre-mature parts failure.
A good example of where poor torque can cause pre-mature parts failure (and other issues) is a head install. Lack of torque will cause a head gasket to leak coolant/oil, which if cross contamination happens (coolant in oil) metal on metal movement and engine damage can occur.
Always torque on the Nut, Never (unless specified or require aka VW/AUDI wheels which use wheel bolts not nuts) Torque on a Bolt head, the overall clamping force is always distributed by the nut as the threads of the bolt will bite into and bind against the material it is threaded into. By torquing a bolt head, you are twisting the head which creates extra resistance on the wrench. This means a bolt that you are trying to torque to 40ft/lbs of force may only have 30ft/lbs of clamping force on it. Torque rates for bolt heads already have this and thread stretch calculated into the rating.
Using anything that extends the distance that the head of the head of torque wrench from point of torque (not a ratchet extension but for example a crows foot that extends the overall length of the "handle") increases the amount of torque put on a nut at any torque rating before the torque wrench will "click". I do not have the current formula on me and will copy it down monday from my General Tool Tech Manual, but you will need to measure the difference and input the desired torque to get what setting you will need to put the wrench at (I may even put up a diagram)
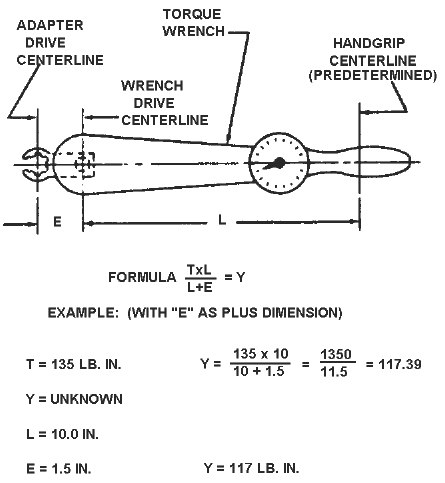
diagram stolen from engineersedge.com
Last thing I can think of, be sure to always double check the ratings and make sure you are following the right ones. It is very easy to accidentally read in/lbs as ft/lbs and vice-versa. I will also put up a metric-imperial (and vice-versa) conversion table when I get the leverage formula.
Torque Wrench 101.
1. General care and Storage:
When purchasing a torque wrench, be aware to look up the manufacturers tolerance. This should be in a (+/- X%) marking. This means that when you set your torque wrench to a given value (e.g. 350 in/lbs) it will be within a range of that setting (a +/-5% tolerance will be anywhere from 367.5 to 332.5 in/lbs when set to 350 in./lbs). Generally speaking anything more than 3% isn't worth purchasing, as the tolerance tend to enlarge over time.
When storing your torque wrench for any period of time (more than 30 mins is a good rule), do not leave it on the torque value you had last used. Instead bring it to the lowest value on it's rating, NOT ZERO. Bringing it to "zero" can loosen the internals and ruin the torque wrench.
Every manufacturer has a set amount of uses per calibration of torque wrench they make. Keep track of this useage, when you are close to that number, or a year has gone by since purchase (which ever comes first) send it to the manufacturer for calibration. The internals weaken over time and need to be adjusted properly, otherwise your +/-2% wrench will become a +/- 10%.
Do not, and I repeat do not DROP even onto a table your torque wrench, even a 1" fall can loosen components and make the wrench un-usable. If dropped accidently, send the unit in for calibration.
2. Proper Application.
When choosing to use your torque wrench, make sure that the wrench is able to stay within torque range. Using the Wrench example as above, a nut that is required to be torqued to 340-360 in/lbs would require a different wrench than above, as the wrench can either over-torque or under-torque the nut and cause pre-mature parts failure.
A good example of where poor torque can cause pre-mature parts failure (and other issues) is a head install. Lack of torque will cause a head gasket to leak coolant/oil, which if cross contamination happens (coolant in oil) metal on metal movement and engine damage can occur.
Always torque on the Nut, Never (unless specified or require aka VW/AUDI wheels which use wheel bolts not nuts) Torque on a Bolt head, the overall clamping force is always distributed by the nut as the threads of the bolt will bite into and bind against the material it is threaded into. By torquing a bolt head, you are twisting the head which creates extra resistance on the wrench. This means a bolt that you are trying to torque to 40ft/lbs of force may only have 30ft/lbs of clamping force on it. Torque rates for bolt heads already have this and thread stretch calculated into the rating.
Using anything that extends the distance that the head of the head of torque wrench from point of torque (not a ratchet extension but for example a crows foot that extends the overall length of the "handle") increases the amount of torque put on a nut at any torque rating before the torque wrench will "click". I do not have the current formula on me and will copy it down monday from my General Tool Tech Manual, but you will need to measure the difference and input the desired torque to get what setting you will need to put the wrench at (I may even put up a diagram)
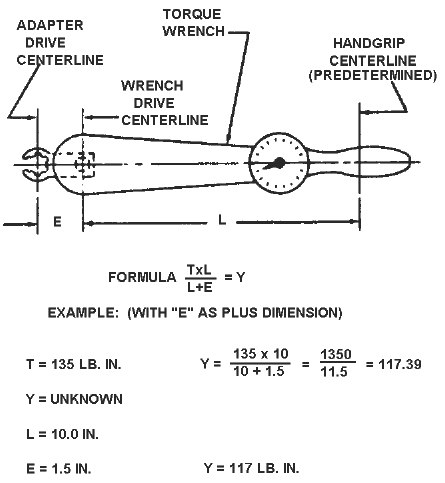
diagram stolen from engineersedge.com
Last thing I can think of, be sure to always double check the ratings and make sure you are following the right ones. It is very easy to accidentally read in/lbs as ft/lbs and vice-versa. I will also put up a metric-imperial (and vice-versa) conversion table when I get the leverage formula.
Comment